Project Management
The project management (PM) module deals with setting-up new projects including all departments, rooms and project specific services. It also assigns delivery phases of the equipment to be purchased as New as well as, assigns transferred items from other facilities to specific rooms in the new project. All project schedules, warranty information, and delivery schedule and project control functions will be performed in the PM module. Project specific specifications are modified in this module as well as assigning budgets by phase. The PM menu includes a comprehensive document control section that deals with documents submittals, documentation of meeting minutes, and status reports. Other project management utilities include assigning shop drawing requirements and controlling the revisions and changes to each room in the project.The PM module provides valuable tools to not only Consultants but also Project Managers and Providers in assigning and managing who is responsible for purchasing, installing and performing the scope of work for each component in the project; thus facilitating the production of coordinated design drawings and reports irrespective of ownership.
Partial List of Benefits:
- Achieve up-to 50% savings of the project management and documentation time by managing the progress of the project online. All organizations (Owners, PM, contractor/EPC, Subcontractors, etc.) working on the projects will have quick access to current documents including drawings, BIM models, contracts, reports, schedules, bids / tenders, and more.
- By assigning the scope of work for each of the FF&E items to a specific Consultant, Project Managers and Providers can benefit from overseeing the entire project; thus removing any gaps and ensuring accountability.
- Controlling cost at every stage will enable Providers to decide on how much and where to spend valuable resources.
- Monitoring and managing the progress of the project will allow for rescheduling of activities, re-allocation of resources and re-prioritizing of work; thus saving money.
- Save time by expediting the response time to carry out actions that need to be undertaken as a result of minutes of meetings.
- By using the Dashboard, tracking of the status of each item in every room will enable decision makers to better manage the project and proactively take actions to make sure that the progress stays on schedule.
- Instead of selecting on the dash board the basis of design for each item in every room, making the selection in one screen for all items will not only save considerable amount of time but also ensure consistency for items belonging to the same Sub-category and Type.
- Reference information and cut sheets relative to basis of design or actual procurement selection will be at the fingertips of architects and engineers.
- Reviewing and approving materials submittals online as well as the shop drawings will save time and ensure centralized documentation. Say no more to hard copies and days wasted in obtaining approvals. Save at least 50% of the time in uploading files and creating transmittals.
- Assigning the correct cost center that will be charged for each piece of equipment per room will help the Finance Departments in allocation of costs and depreciation.
- Save time by generating all the documents needed to apply for Certificate of Need (CON) from governing bodies.
- Utilizing online electronic specifications that are consistent with the design will not only save time but will also ensure accuracy and transparency.
- Retrieving up-to-date drawings from the central cloud based and view in 2D and 3D will enable all parties to access the most up-to-date project drawings. All revisions will be recorded and can be tracked as they are issued.
- Use of mobile devices onsite to monitor and record work progress and report snags or punch lists on the spot will save time and ensure that the concerned parties respond quickly.
Project Planning
Populating items or assemblies in each room is performed in the Pequip Planning Module. Rooms can be automatically populated by importing a project, a department or a room from another project or from a template. Deletion of items in a room is also performed in the same menu. The user can assign the quantities per phase of items expected deliveries or as existing items in the project resulting from transfers from other estates.
A helpful feature of Pequip is the ability to add or delete an assembly to multiple rooms in the project in one simple screen.
Partial List of Benefits:
- Applying the concept of Components and Assemblies (Unions) will ensure that each component attributes will be captured and will be reflected independently on the design drawings. Building assemblies like cabinets and large systems will avoid creating new item descriptions that say “This component is part of another item” and will facilitate procurement from the proper source in order to save cost.
- Accessing and editing component information from the planning menu will save time from needing to switch screens to the products management menu.
- Being able to add or delete an item from multiple rooms will save time and ensure standardization in programming.
- Once the user’s works on one or more projects in Pequip, irrespective if the subscription is for a single project, all projects information from previous projects will be retained in the independent users database account. This will allow for copying old projects, departments or rooms into the new project, thus avoiding starting from scratch. This is in addition to being able to copy templates that are developed by the individual accounts or from the global templates, as well as importing Excel spreadsheets to the database.
- Incorporating device integration requirements and IT requirements of the equipment during the planning stage will ensure that the facility will be designed to accommodate all IT active and passive components.
- Instead of relying on BIM applications to generate BOQ, REL and other reports, these reports will be readily available in the planning module including calculations of electrical consumption for all equipment.
- By cross referencing the Pequip item numbers with the original item numbers supplied by the Owner, customers will benefit from being able to display the original item numbers.
- Transitioning from generic planning to detailed planning incorporating more specific descriptions with details such as mounting requirements will ensure consistency of information in accordance with the project brief.
- By having electronic specifications built-in the planning module, customers will benefit from developing generic specifications that are customized for each project.

Design
Pequip is fully integrated with AutoCAD and integration with REVIT is underway. All components, blocks or REVIT Families, instructions, plug-ins, other rooms services and project information that are stored in Pequip will be imported to AutoCAD. Because of the AUTOCAD and REVIT integration, equipment planners can focus on the proper location and placement of each item in each room without being fully trained on CAD. Every aspect of the coordinated loaded drawings including title blocks, schedules, drawing information, loading list, blocks and services will be automatically populated with a few commands; thus allowing AutoCAD trained staff to focus only on dimensioning and elevations. Typical drawings will be copied from the master rooms when users identify the typical layouts in the design module. Multiple rooms can be combined is a single drawing, once identified as such in Drawing Register and Document Menu. Even exploding using X-ref from individual blow-ups to the 1:100 floor plans is performed automatically in different layers. Generating and developing a complete loaded drawing will take at least 70% less time than the manual process while consistency between the drawings and the reports will be guaranteed because of the built-in bi-directional interface.
Partial List of Benefits:
- Integration between Pequip and AutoCAD or REVIT will save customers 70% of the time it normally takes them to generate design drawings manually.
- Bi-directional interfaces will ensure consistency of information between the planning phase and the design drawings.
- Attaching objects of outlets for all electromechanical, IT and other services to the AutoCAD block or REVIT model will not only ensure proper allocation of services in the room drawings but also accurate capturing of this data.
- Providing specific site requirements and instructions for design in the design module, such as mounting height, will enable draftsmen to locate all outlets in the rooms while planners will focus on where to place items in the rooms. Hourly rates of planners and architects are significantly more than draftsmen.
- Connecting the functional programming with the planning module and the design model will ensure compliance with the Owners project brief.
- By keeping all parameters, characteristics, attributes of each item (regardless of ownership) in the Pequip database acting as the BIM library, users will benefit from having a lighter BIM model which make REVIT work faster and more efficient. There wil be no need to store all of this information in the BIM model as Pequip can generate all of the reports including exporting to IFC and COBie.
- While tracking can be done in BIM, a better way of tracking will be done by Pequip because we can identify “who” made the change based on who signed in and also “Why the Change was made.
- Viewing BIM models in a browser and on mobile devices will enable non-BIM experts to easily maneuver through each room and provide mark-ups, overlays and real-time comments.

e-Tendering
Pequip manages the entire procurement cycle in the e-tendering module by addressing every involved work procedure starting from assigning components to packages or requisitions and ending with suppliers submitting online their qualifications, technical and financial offers for specific tenders or Requests for Quotations using the dedicated vendors’ portal. E-Tendering adapts to how business is conducted in many parts of the world where selection is made after a formal process of tendering and before final construction drawings are developed. Pequip also addresses less formal means where products make and model are pre-selected during the design stage of a project. The system also accommodates awarding tenders based on primarily price and the provision of proposed approved manufacturers thus deferring the selection of the final products make and models to the Materials Submission stage during the construction period.
Partial List of Benefits:
- Management of vendors, packages, tenders and contracts will be performed much more efficiently by replacing the old paper based system or using Excel sheets with digital versions, automating processes, and keeping all data in one place.
- Submission of proposals using the Online Vendor Portal will save a significant amount of time ensure accuracy. The same data entered on the portal will automatically appear in Pequip to be used by evaluators, project managers and providers; thus avoiding duplication of effort.
- Online correspondences between the Owner / Consultant and each vendor will expedite the response time and document all transactions.

Evaluation
The process of tender evaluation will involve different stakeholders utilizing the Tendering Evaluation module thus enabling Pequip to process evaluations and facilitate the selection of vendors in very quick time frames and in utilizing very objective, unbiased and consistent methodologies. Verification of all technical offers that are submitted online by the bidders is very easy and can be performed by multiple technical experts at the same time, thus saving time and ensuring accuracy. Pequip will automatically tabulate the technical and financial results and will convert the total scores into percentages according to the weight given to each. Furthermore, evaluation of bidders’ capabilities and qualifications is taken into consideration and will be factored in the total final scores, thus providing a balance between technical, financial and the abilities of the vendors’ to perform the scope of services. All communications with the bidders is conducted online via a documented RFI process.
Partial List of Benefits:
- By having multiple evaluators perform technical evaluations online at the same time, the total evaluation period can be reduced by 70%. All offers including supporting catalogues and cut sheets are available in digital format thus saying good bye to hard copies and paperwork.
- Financial calculations, comparisons and evaluations will be performed by Pequip in seconds by extrapolating the financial offers posted by each bidder on the Vendor Portal. Including the cost of all options and accessories as well as splitting the cost of freight and customs will capture all of the OPEX and APEX costs in the total calculations. Suppliers will not be able to hide costs of optional items as these will be clearly identified early on.
- Factoring each Bidder’s capabilities, past experience and abilities in the total evaluation criteria will ensure that Customers consider the best value for the money based on a technical, financial and company capabilities.
- By forcing bidders to enter all information in the portal, the customers can ensure that they will receive complete offers based on uniformed standards and expectations. This will avoid needing to go back to each bidder for clarifications and ensure unbiased evaluations. .
- Since evaluators will not have access to pre-assigned scores and weights of the specifications during the evaluation process and will only need to verify the responses, enter their comments, and provide percentages of compliances; customers will be assured that the evaluation is being performed in a very scientific, objective and transparent manner.
- Giving access to Providers to review all evaluations online and to actively perform their independent verifications will provide more checks and balances to ensure objectivity and transparency in the process. Proper documentation will facilitate proper auditing by third parties.
v
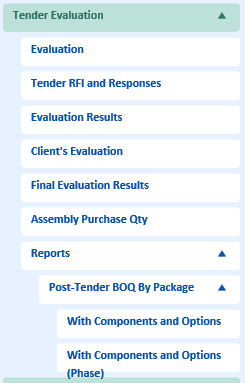
e-Procurement
The Procurement Module covers all of the workflow required to develop and issue comprehensive electronic purchase orders. The work process normally involves ensuring that all standard options, accessories, disposables, consumables and spare parts are included in the order. Following that, negotiations with bidders is facilitated using the online vendors’ portal. Upon the successful negotiations, selections can be made for each component in a package or requisition. The complete selection will then be automatically populated in the purchase orders which can be migrated to an ERP system. In addition to the standard PO format, Pequip will capture all warranty requirements, all shop drawings requirements, and will segregate OPEX vs. CAPEX elements thus allowing for accurate receiving, invoice payment approvals, and depreciation of the capital equipment. In some countries where sales tax is applicable, the PO will automatically calculate the amounts based on a percentage that will be recorded in the Project Set-Up Menu. For contracts that require future materials approvals and selection, amendments of purchase orders is possible to add exact make, models and options and accessories.
Partial List of Benefits:
- By linking the procurement process with the project schedule, customers can better plan when they should we make the selection of the Architectural Significant Equipment so that the site will be prepared according to specific make and model requirements. This will avoid needing to tear down walls and make site modifications after construction was completed.
- Customers can better plan when they should issue purchase orders based on room readiness.
- Including all details in the purchase orders and covering all project requirements will not leave room for future variations.
- By having Pequip generate comprehensive purchase orders, all PO data can be easily migrated to the customers ERP system.
- Bundling items in tender packages will facilitate getting more competitive offers and reducing total cost to the customers.
- Aggregating equipment purchases will optimize capital spend volume, and achieve subsequent discounts.
- Consolidating shipments will further reduce total costs as freight cost can account to 20% of the total cost.
- Differentiating between capital cost that is depreciable and operating cost such as freight, taxes, customs, consumables and disposables will recognize expenses in the proper chart of account.
- Accessing Group Purchasing Organizations pricing, local, regional, national and/or government contracts that is available to the facility can reduce procurement costs.
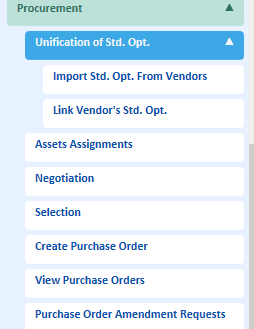
Execution
Because Pequip database was designed to be a fully relational and integrated from the stage of project planning to the design stage and then to product evaluation, selection and procurement; having a built in Execution module makes the program much more powerful because the data required for implementing the project can be easily retrieved from other modules to enable effective and efficient project management. The Execution module covers the entire construction stage workflow including Materials Submittals, Shop Drawings Approvals, products Receiving, Installation, Commissioning, Products Hand-over and even Asset Management. Should a Client desire to use the Execution Module for implementing products that are not under scope of work of the Consultant, then a manual purchase order must be generated in Pequip for those items which will enable receiving and installing these items using Pequip. These items should also be included in the room planning menu under Project Planning so that installation can be performed in these rooms and so that assets can be registered after commissioning. During the Materials Approval stage and at the client’s choice during other stages, an approval hierarchy is available for Facility Managers to approve what is being recommended by the Consultant. Automatic notification via email will be sent to the approving authorities asking them to electronically approve the transactions; thus enabling a paperless environment for the entire process.
Partial List of Benefits:
- By using Pequip to effectively manage thousands of items being received, warehoused, inspected, installed and commissioned, customers can be assured that that there will be no delays in the project schedule due to FF&E implementation. Pequip will ensure a seamless transition from project to a functioning facility.
- Proactive management of contractors’ performance according to contracts will safe guard against unexpected delays in deliverables.
- Approval of payments to suppliers against deliverables will provide supporting documents to the Finance Office to pay invoices as per the payment terms on the purchase orders.
- Early inspection of received items will prevent delays and will force corrections to be made and replacements to be provided by the suppliers before installation actual begin.
- Tagging the received cartons at the customers’ warehouse will enable tracking the location of orders and timely scheduling of deliveries to the facility.
- Knowing firsthand what was installed and commissioned and what was tested and calibrated will expedite room handover to the customer.
- Knowing firsthand which staff received operational and service training and the availability of O&S manuals will ensure operational preparedness.
- Accessing site construction progress information online and reporting snags or punch lists while on site will expedite undertaking corrective actions by contractors and saves time in reporting.

Estate and Asset Management
The Estate and Asset Management module allows facilities to not only document the inventory they have on hand in each space but also evaluate the conditions of these assets in order to determine of these assets are in acceptable working condition to transfer to another space in the same facility or even to another facility that is owned or operated by the same Estate. The Asset Management module captures valuable data on all assets in all facilities belonging to the same Estate including history of each item, current status per item, date put into service, validity of warranty and start date, estimated useful life, preventative maintenance schedules and asset management depreciation values.
Partial List of Benefits:
- Documenting the condition of existing inventories will facilitate making prudent decisions on what can be re-used and transferred to other facilities; thus saving money on future purchases and better planning for future service support.
- Identifying each asset in the estate and in every facility will provide Facility Mangers valuable tools not only to manage all assets but also to get historical records from the beginning of each project.
- Before transitioning to a Clinical Engineering Program, Facility Managers can ensure that barcodes have been placed on all equipment at the time of installation.
- By having updates as to when each piece of equipment was placed in operation, Facilities Managers can manage when the warranty begins, service start date and what is covered.
- By forcing suppliers to input preventative maintenance schedules as part of the handover process, Facility Managers will save time in manually posting this data as it will be an integral part of the Asset Management System.
- The Accounting Department can recognize asset values for depreciation and financial reporting without having to manually gather this information.

Templates and Drawings
The Templates Module provides users with the ability to view templates of projects consisting of departments, rooms and items and to also view templates used by other organizations, provided that the item numbers get matched with the users’ item numbers in their respective databases. Manufacturers can also post their templates and link their products to items already in the catalogue database. In addition to showing the lists of items typically belonging to a room in a department, any AutoCAD room drawing or PDF version can be viewed and saved on a standalone computer. Users have the ability to view all components’ information including specifications, physical characteristics, plug-ins and other information that is available in the Products Management menu. Manufacturers’ product data that are linked to each item can also be viewed from the same screen.
Currently, P Equip has templates belonging to several healthcare departments and multiple rooms.
When using the Design Module, room templates that are created in BIM can be imported to a temporary BIM project where all the departments and rooms can be assembled to create families and an entire project model. The model can adjusted according to the project program and then viewed from a mobile device. The entire model can be linked with REVIT and the Pequip database for bi-directional integration.

Products Management
The Products Management section of Pequip is where all the products data are stored in the database.
The Products Catalogs is where accounts or manufacturers, using the Manufacturers Portal, will upload all their catalogs and datasheets by Category, Subcategory and Types as well as their specifications, Images, Electromechanical requirements, Pricing, Options and Accessories, Documents and REVIT or AutoCAD blocks, and other information. Users can compare specifications and products information from multiple manufacturers and multiple models. The Manufacturers’ Products catalogue can be filtered by description, manufacturer name and other fields for ease of searching and management and each item can have an image associated with it.
Manufacturers’ catalogs will be matched with specific components in the Pequip database as one catalog can apply to multiple components. Once, the matching is done, the selected catalogs will be displayed in the Component Screens as one being used by the specific account. This will enable each account to decide on what to see as catalogues for their projects instead of having to view hundreds of catalogs.
In the Project Management menu for each project, users will view all catalogues per Category, Sub-category and Type and can decide on which ones select as “Approved Manufacturers” for each specific project. Users can also select one per component that which is use as a “Basis of Design” or pre-selection as an approved draft manufacturer and model number.
The Assembly / Components section of Pequip is where all the products data are stored in the database along with their categories, classifications, attributes, specifications, plug-ins, active manufacturers, mounting, physical characteristics, standard and optional accessories, etc. Pequip treats each item as an “Assembly” with “Components”. This is consistent with how REVIT works having Families with individual components to make up a complete system. An Assembly can only have one Component or can have a group of multiple components comprising a complete unique system. Each component AutoCAD block or REVIT model is stored in the Component Menu along with other documents that facilitate the integration with the design drawings.
A host of reports are available to facilitate the management of all Assemblies and Components and to provide tools for users to identify missing information that needs to be completed.
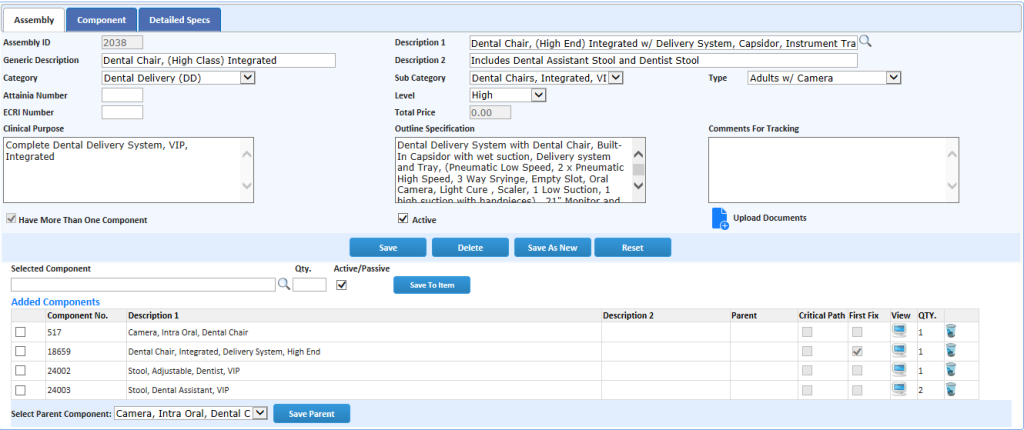
Manufacturers Management
Manufacturers can be added by the Users directly in the Pequip Manufacturer Management module or through the website upon completion of registration procedures.
Once the Manufacturer will be registered, an email will be forwarded providing the user name and the password for that manufacturer The manufacturer will then login using the dedicated portal.
Manufacturer Portal:
The manufacturers will be able to complete and always update their profile on line. Will be able to provide specific information on their products such as Specifications for each, categories, sub-categories and types that their products belong to, model numbers, certifications, Group Purchasing Membership, List Prices, Services connected with each component, physical characteristics, options and accessories as well as attach catalogues, cut sheets, marketing material, AutoCAD blocks, BIM models and other material. All of the data submitted by each manufacturer will first be reviewed for accuracy by the Pequip Users and then will automatically get posted in the Pequip Products Catalog.
Partial List of Benefits:
- By having manufacturers post their catalogues and products data free of charge directly in Pequip, customers will avoid needing to visit other websites or to subscribing to other programs in order to perform technology comparisons.
- Instead of browsing through hundreds of products by different manufacturers, users can customize the number of products they want included in their independent database.
- Accessing the assemblies and components menus from the planning screens or the design screens will save time from needing to switch between menus to review attributes and make modifications.
- Storing all characteristics, generic specifications, attributes, geometries, options and accessories, manufacturers’ data, design BIM models, AutoCAD blocks and design instructions all in one menu enables comprehensive management of each item.
Vendor Management
Pequip treats manufacturers separately from vendors in that in most countries, procurement is done with local distributors and dealers. New vendors are registered in the Vendor Management Module and all information can be entered either manually, migrated in from Excel sheets or automatically updated once Vendors enter their data in the Vendors Portal. All questions that Vendors will need to complete and submit relative to their past experience in performing similar work can be will be created and customized in the Prequalification Questionnaire Screen. Once answers are entered, users can view online the Vendor’s Profile, prequalification profile, and answers to project specific prequalification questions. Based on submitted qualifications and capabilities, Pequip will create an Excel exportable comparison table showing the data provided in comparative columns for each vendor that identify the number of employees per organizational level, annual revenue and list of previously performed turnkey project. Another exportable comparative table identifies the names of the manufacturers each vendor represents per subcategory as well as how service is being rendered for that manufacturer (In house or Outsourced). All of this online information will facilitate rating the capabilities and abilities of each vendor in performing the scope of work for a specific tender.
Pequip Vendors Portal
The vendors’ portal is divided into five sections. The first is the Vendor’s general information which included the Vendor Profile and the Vendors Manufacturers information. The second is project specific whereby information on the specific project will be automatically published from the Project Set-up menu and whereby companies can complete the two forms for the Vendors qualifications and capabilities to undertake specific projects. The third has to do with specific Tenders whereby the Vendor will select the RFP he / she has been approved to participate in, will submit all technical and financial offers, will submit RFI’s to the Consultant, will respond to clarifications issued by the Consultant, and will submit price reductions that may be required as a result of negotiations. The fourth has to do procurement where the companies can view and accept purchase orders. The fifth has to do with the execution part of a project whereby the vendor can upload and electronically transmit all shop drawings, materials submissions including compliances with the specifications and catalogues, and other documents related to after the sale service. Vendors can also view the status of their performance and progress in a project.
System Administration
The system administration section of the Pequip program includes the root tables that drive the entire system. All categories, subcategories and types that define each assembly and component are defined in this section. So are the groups, mounting types of the equipment, and providers. The electromechanical, IT and Audiovisual services that may possibly be used as plug-ins or independently in rooms are specified along with the respective AutoCAD blocks and REVIT models.
Setting up authorization and access levels of users is restricted to the administrator of the program in order to separate the responsibilities of each user. The customer can customize access levels to each menu and screen according to the set responsibilities.
Other data that is not related to working on projects is available in the system administration section such as maintaining information on other projects, tenders or other databases and previous prices.